Collaboration Is Key to A Strong Materials Discipline
NASA has a strong need for advanced materials and processes (M&P) across the realms of robotic- and crewed-spaceflight, as well as aeronautics, particularly when one acknowledges that all craft must be made of something. To meet that need, the materials discipline relies on collaboration—both between centers and across disciplines. Reaching the Agency’s Moon-to-Mars objectives will require leveraging each center’s specific M&P expertise, cross-training among the centers, and routinely interacting with the 20-plus Agency disciplines like structures, space environments, and loads and dynamics. When a discipline touches all classes of materials; all aspects of design, manufacturing, testing, and operations; and all phases of flight, collaboration is the only way to broaden and deepen its reach.
This year, the Materials TDT pulled in wide-ranging center and discipline support for the VIPER lunar rover, investigations of cracks in the ISS Russian PrK, the X-59 supersonic aircraft, and the SLS Program. It also leveraged its contamination control experience to aid the Commercial Crew and Orion Programs. Below are some additional highlights from the year.
Collaboration Among Disciplines
Ms. Alison Park, NASA Deputy Technical Fellow for Materials, led a multi-disciplinary NESC team to address JPL’s request for sup – port to investigate anomalous temperature readings during thermal vacuum testing of the NASA Indian Space Research Organization (ISRO) Synthetic Aperture Rader (NISAR) reflect-array hardware, already integrated onto the spacecraft in India. The team provided detailed reviews of the thermal models and supported materials testing and characterization of the reflect-array construction record. The team’s work identified operability concerns from higher than expected temperatures that would be seen during the multi-day deployment process. The hardware was demated from the space – craft and returned to the United States for design upgrades and modifications to address the new concerns. The hardware is now set to return to India for reintegration and final launch preparations.
Fostering Intercenter Cooperation
Mr. Robert Carter, NASA Deputy Technical Fellow for Materials and GRC Deputy Division Chief, attended a technical exchange between GRC and MSFC. The exchange uncovered the need for an Agency-wide, materials-driven alloy development plan to identify key needs that would benefit spaceflight and aeronautics. From there, materials representatives from 7 of the 10 centers met in-person to develop a roadmap and a plan to be released in FY25. The Materials TDT also stood up an Alloy Development Community of Practice to provide a grassroots mechanism to identify cross-Agency needs, technical challenges, and benefits that aren’t identified programmatically or within mission directorates.
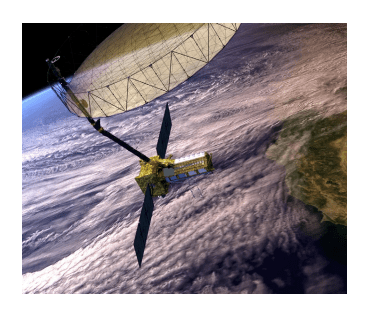
Leveraging NASA Partnerships
The NASA Technical Fellow for Materials, Dr. Bryan W. McEnerney, hosted visitors from the European Space Agency (ESA) for a combined trip to JPL, GRC, and KSC, as well as the jointly organized Worldwide Advanced Manufacturing Symposium (WAMS) in Orlando, FL. In-depth technical interchanges between NASA and ESA emphasized advanced manufacturing with a focus on spaceflight needs. The event increased technical collaboration be – tween the two organizations, leading to ESA’s request to NASA for a formal review of ESA’s stress corrosion standard. Work was also initiated on a joint NASA/ESA intern program. Next year brings a number of new and exciting challenges, including an elevated temperature testing program focused on HallPetch effects in C-103 (niobium alloy), the domestic North American WAMS symposium in Knoxville, TN, and a continued focus on intercenter technical support. And, always a key objective, the discipline will actively engage early-career personnel on NESC assessments to learn from our veteran materials experts and to pass on the knowledge so unique to the space industry.
from NASA https://ift.tt/C0dP6sK
via IFTTT